Friedrich Eisenkolb Accredited Testing Laboratory
Competent, fast and flexible
General
More than 60 years ago, our eponym, Prof. Friedrich Eisenkolb, laid the foundation for our powder-metallurgical test laboratory in Thale, Germany. We carry out physical, mechanical-technological and analytical testing at metallic and powder metallurgical materials as well as testing of metal powder and testing of technical cleanliness.
Our team of 9 employees guarantees technical competence at the highest level and ensures promptness and flexibility for the solution of complex material-testing tasks.
Our laboratory is a certified training organization for material inspectors.
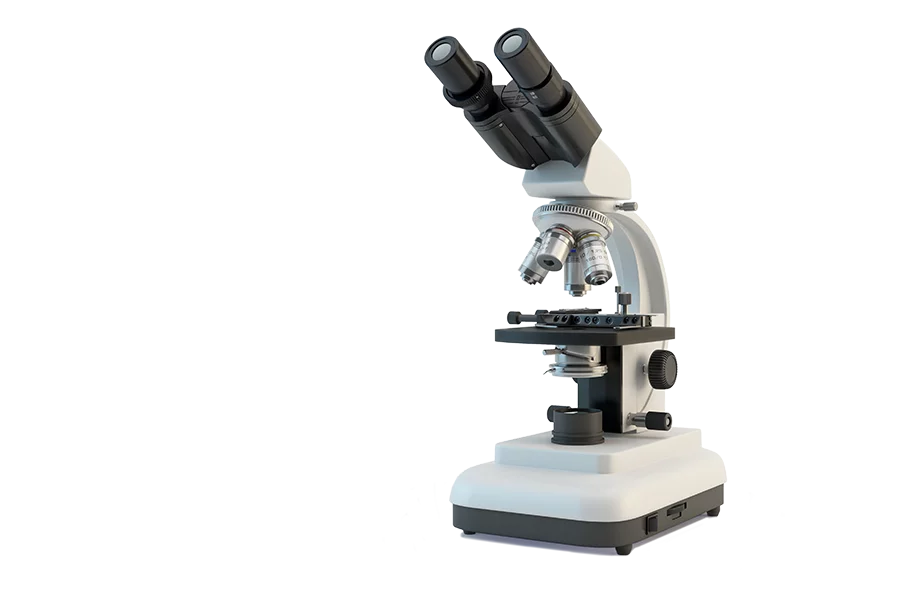
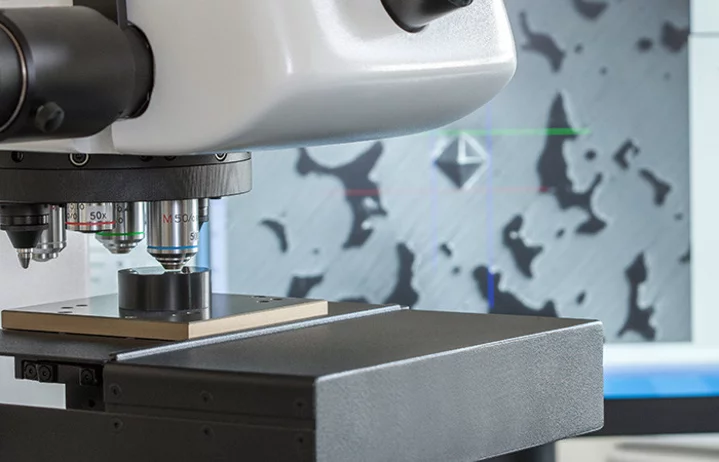
Mechanical-technological testing
- Tensile test at room temperature and up to a maximum of 1.100 °C, bending test, compression test
- Determination of Charpy and ASTM notch impact strength; RT to - 196 °C
- Brinell, Vickers and Rockwell hardness testing; small-load hardness, hardness-displacement-curves, micro-hardness testing
- Technological tests on components in accordance with requirements
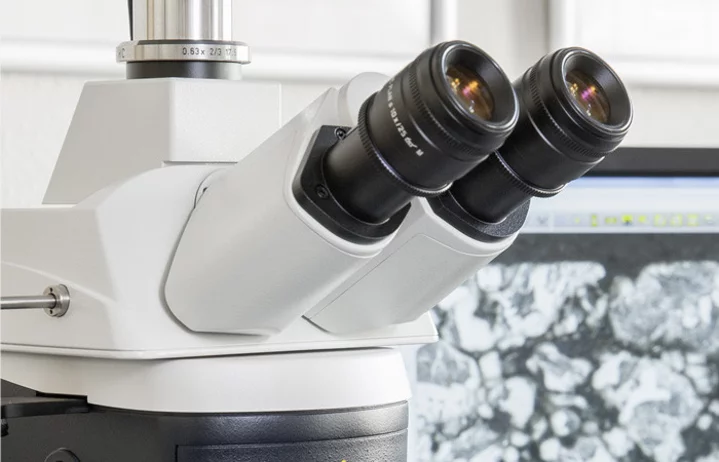
Metallography
- Macro and micro analyses
- Sinter materials
- Castable materials
- Fe materials low-alloy to high-alloy
- Non-ferrous metals
- Heat-treated parts
Damage inspections:
- Digital image analysis
- Determination of phase fraction
- Particle-size analyses
- Coating thickness measurement
- Graphite size determination in accordance with DIN ISO 945
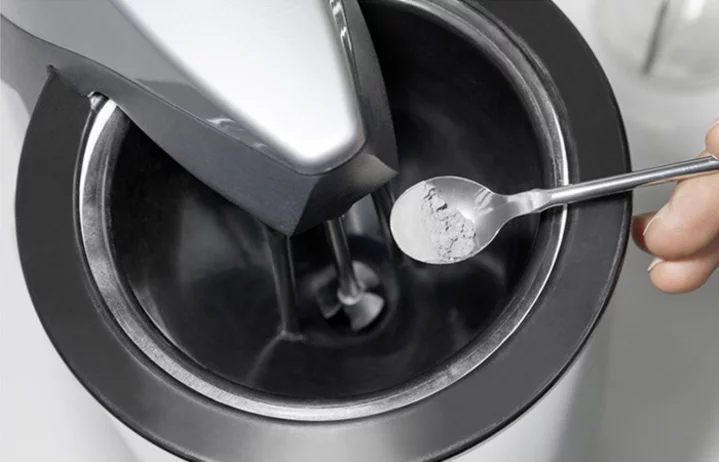
Powder testing
- Determination of grain-size distribution with a laser grain-size analyzer (0.01µm bis 3500µm)
- Determination of tap density
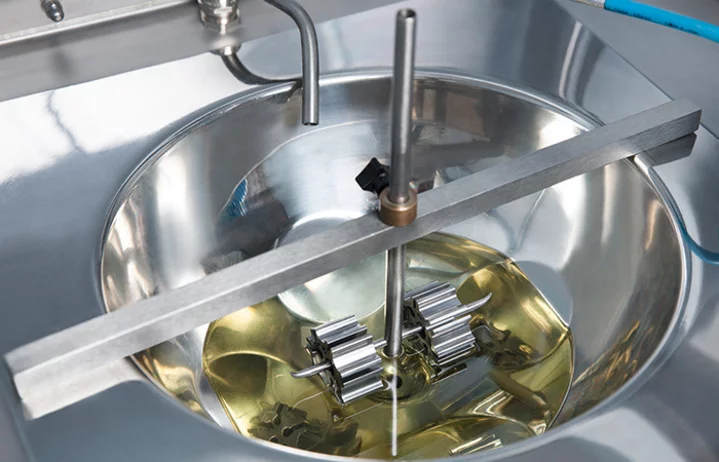
Test of technical cleanliness
- VDA-Guideline 19 Part 1 (Test of technical cleanliness – particle contamination of functionally-relevant auto parts),
- ISO16232 (Road vehicles – Cleanliness of Components of Fluid Circuits)
- In accordance with plant standards of automotive manufacturers and suppliers
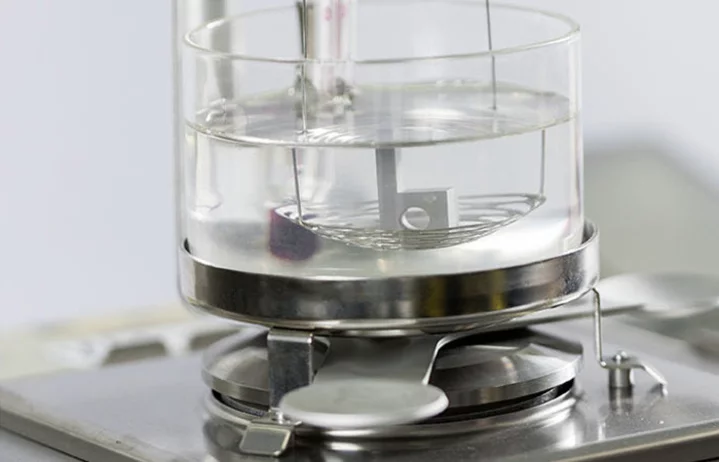
Physical testing
- Density determination: immersibility density
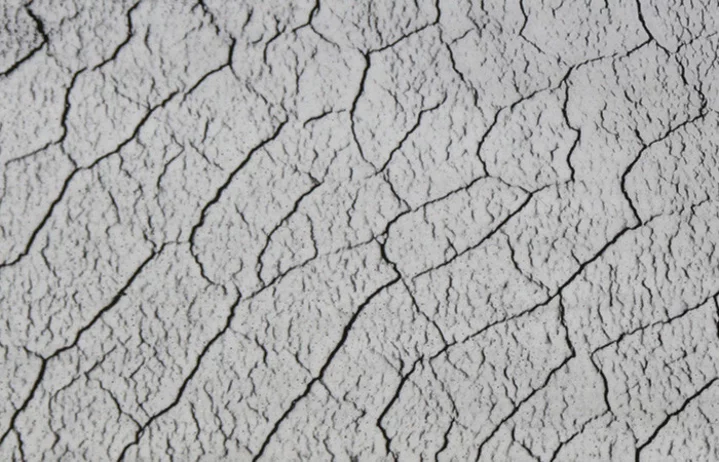
Non-destructive material testing
- Surface crack testings
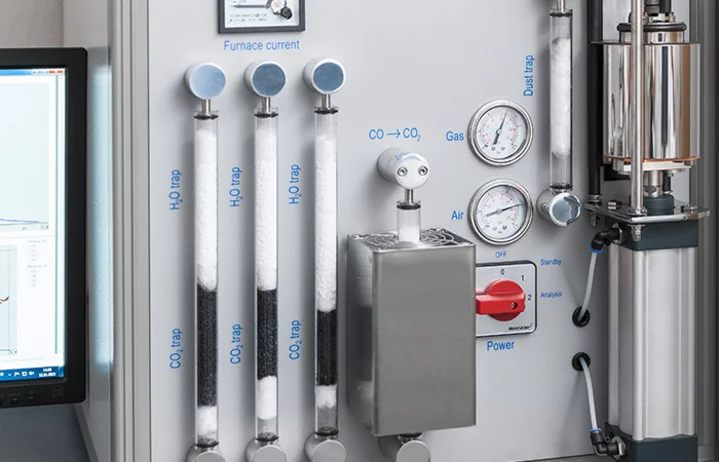
Chemical analysis
- Analysis of compact samples with OES
- Determination of carbon and sulfur with CS- analyzer
- Determination of oxygen and nitrogen contents in metals
- EDX analyses
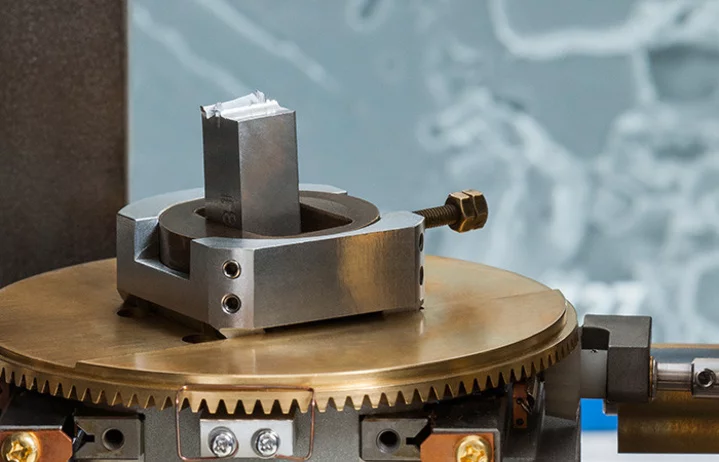
Scanning electron microscopy
- Fracture surface analyses
- Damage analyses
- Microstructure analyses of metallic and non-metallic materials
- Length measurement in micro range
- EDX analyses
- Element distributions (line scans, mappings)
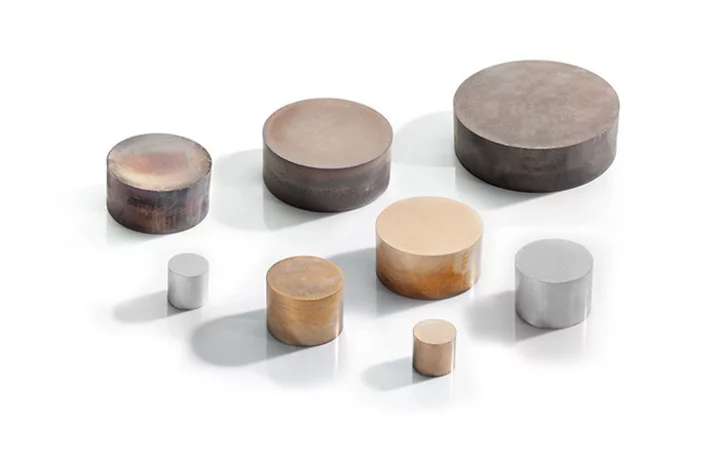
Metal-powder blanks for prototype production
- Presses with floating dies
- Diameters of 58, 80, 100 and 130 mm
- Maximum height 42 mm (depending on density)