Pilot project mining - Smart Charging in the heavy duty sector
Schunk Smart Charging is already in use worldwide as a charging solution for electric buses. But the potential applications of the conductive and wireless charging system are far from exhausted. The technology is also demonstrating its potential in the automated charging of battery-powered mining vehicles. Product Manager Timo Staubach explains the background to this globally unique pilot project.
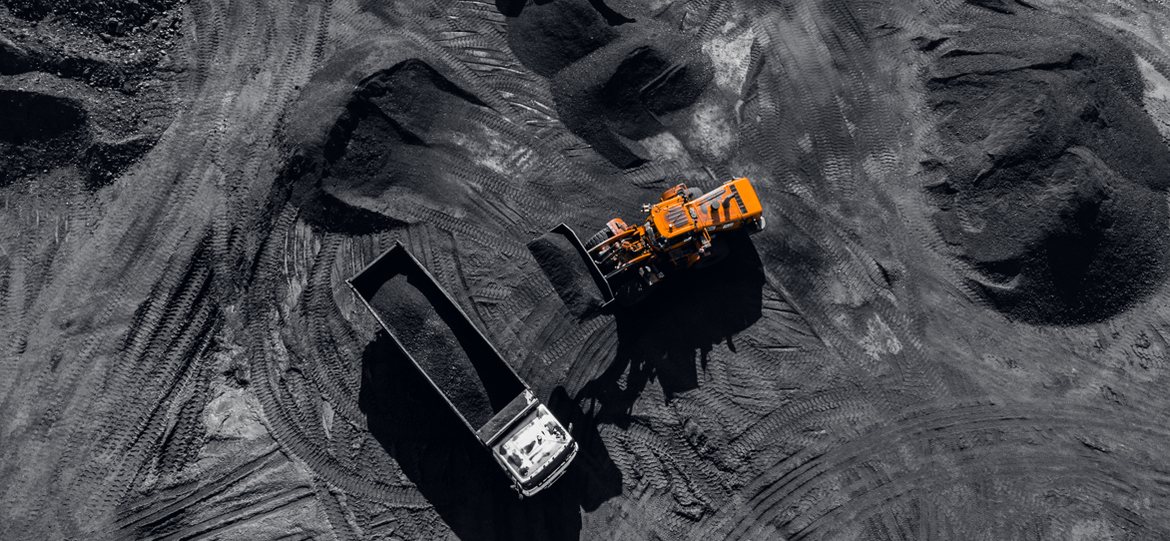
What advantages does Schunk Smart Charging offer as a charging system for industrial electric vehicles?
Timo Staubach: From the very beginning, we were aware that our Schunk Smart Charging solution can be applied in more sectors than just public transport. Battery-powered vehicles in ports and mines are a good fit for the system – here, too, the vehicles operate on fixed routes within a limited area. Using electric drives prevents emissions of large quantities of pollutants and drastically reduces fuel costs in this case too. If the vehicles also drive and charge autonomously - as in our pilot project with VOLVO CE - then personnel costs also decrease considerably.
Where exactly was Schunk Smart Charging deployed in this pilot project?
Timo Staubach: The demonstration project’s motto was “The Electric Site,” and its aim was to electrify and automate a gravel mine near Gothenburg to the greatest extent possible. VOLVO CE has been working on this project with other companies and universities since 2011. Schunk Smart Charging comes into play for charging the battery-powered transport vehicles. These transport the rocks in the mine, drive completely autonomously via GPS control, and are also automatically charged at their charging station during operation.
In electric buses, the pantograph or counterpiece sits on the roof of vehicle. Did you have to find another solution for the mining vehicles?
Timo Staubach: In this case, installed the charging counterpiece in the underbody of the vehicles, where it is sufficiently protected. When the vehicle is positioned at the charging station, the underbody charger rises from the ground and connects with the counterpiece. The vehicle’s batteries are then charged with around 200 amps in just five minutes.
Was the test run of smart charging as a charging solution for mining vehicles successful?
Timo Staubach: Absolutely! Fifty percent greater fuel efficiency, 40 percent lower operating costs, about 70 percent less energy costs, and a 98 percent reduction in CO2 emissions. These are impressive results. The 12-week demo operation has clearly shown that combined with automated rapid charging, the electric drive can be the technology of the future – even when subjected to extreme conditions and high safety requirements.
The success of the pilot project in figures