Power plant operators benefit from after-sales service
With decades of know-how in materials and an understanding of the special requirements in various industries, we develop trailblazing solutions together with our customers. The delivery and installation of our products is by no means the end of our involvement with the customer. The visitations of our Scandinavian colleagues to a total of six different hydro power stations provide an example of how our customers also benefit from our extensive experience through after-sales service.
→ Learn more about our solutions for power plants.
Learn more
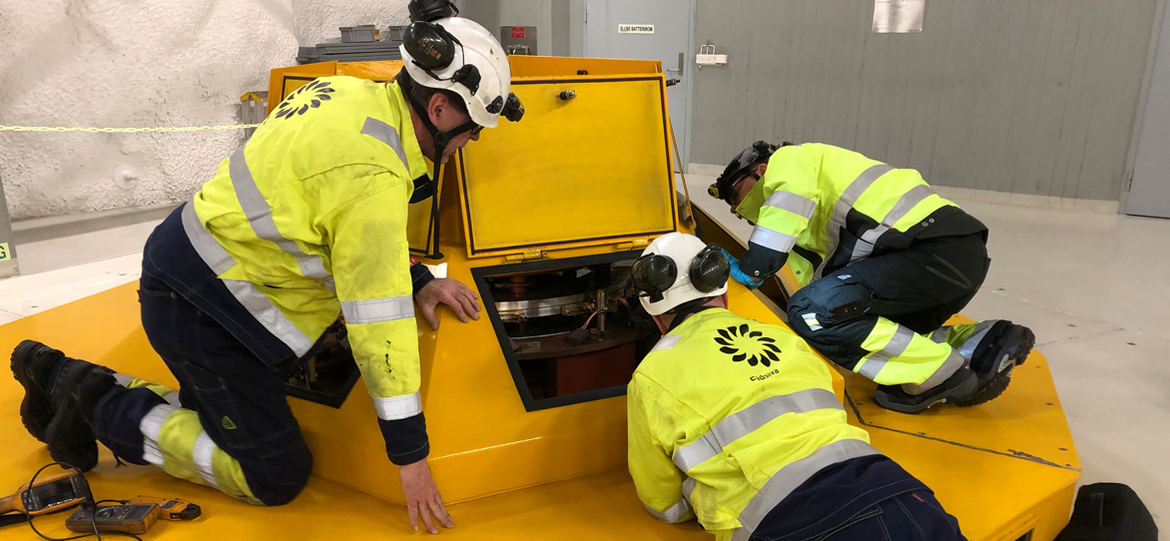
This is why regular on-site inspections are crucial for the operational reliability of power plants
Carbon brushes and slip rings play a decisive role in the efficient and reliable generation of electricity in power plants. Because these parts have to continuously withstand long-term stress, regular inspections are highly advisable. This serves the purpose of function monitoring on the one hand and also provide the opportunity to observe the performance of Schunk products in the field and thus to further optimize them on the other. Exactly these things were the objectives of Pär Wallmark, Business Area Manager at Schunk Carbon Technology Sweden, Application Engineer Anders Törnström as well as other co-workers. They visited Norwegian power plants of the companies of Glitre Energi and Eidsiva Vannkraft, in which carbon brushes developed by Schunk are used.
After-sales service in Norwegian power plants
„Our customers asked us to inspect the selected combination of carbon brushes and slip ring and to provide improvement suggestions“, explained Pär Wallmark. „In such cases we can very often make optimizations which increase the reliability and efficiency of the systems. “Such modifications can, for instance, consist of altering environment parameters such as temperature and humidity or optimizing the material composition of the carbon brushes. The latter not only enhances productivity but also reduces the accumulation of abrasion dust, which can cause increased maintenance costs and expensive machine downtime.
Do you want to avoid expensive downtime?
→ Find out how you can optimize the operational safety of your systems with our brush dust extraction system. Download broschure.
Inadequate materials mean that the carbon brushes need to be changed more frequently.
Quality of materials decisive for maintenance effort and costs in power plants
To try to save money by skimping on brush material can become quite expensive – this is also stressed by Pär Wallmark: „Inadequate materials mean that the carbon brushes need to be changed more frequently. That leads to rising material costs and above all production stops. Moreover, the systems have to be cleansed of abrasion dust more often. And if you neglect to do that, you even risk incurring a short circuit in the motor or generator.“
In the course of their inspection visit, however, our experts did not only examine the Schunk parts which had been installed in the systems. Their respective counterparts, such as commutators and slip rings, can also be subject to mechanical or electrical wear. „We want the best possible efficiency and reliability for our customers“, concludes Pär Wallmark. „And the feedback of our customers shows that we are really good at achieving this.“
Interested in more information?
→ Find all relevant brochures and documents on the topic here. Download now!