Complex shapes, high quality and numerous sizes from RBSiC
Ceramic solutions from Schunk keep going when other materials throw in the towel. The IntrinSiC® 3D printing technique makes it possible to manufacture highly-complex ceramic structures while using silicon carbide (RBSiC) with its nearly diamond-like hardness – thus creating new applications for even the most demanding of customers.
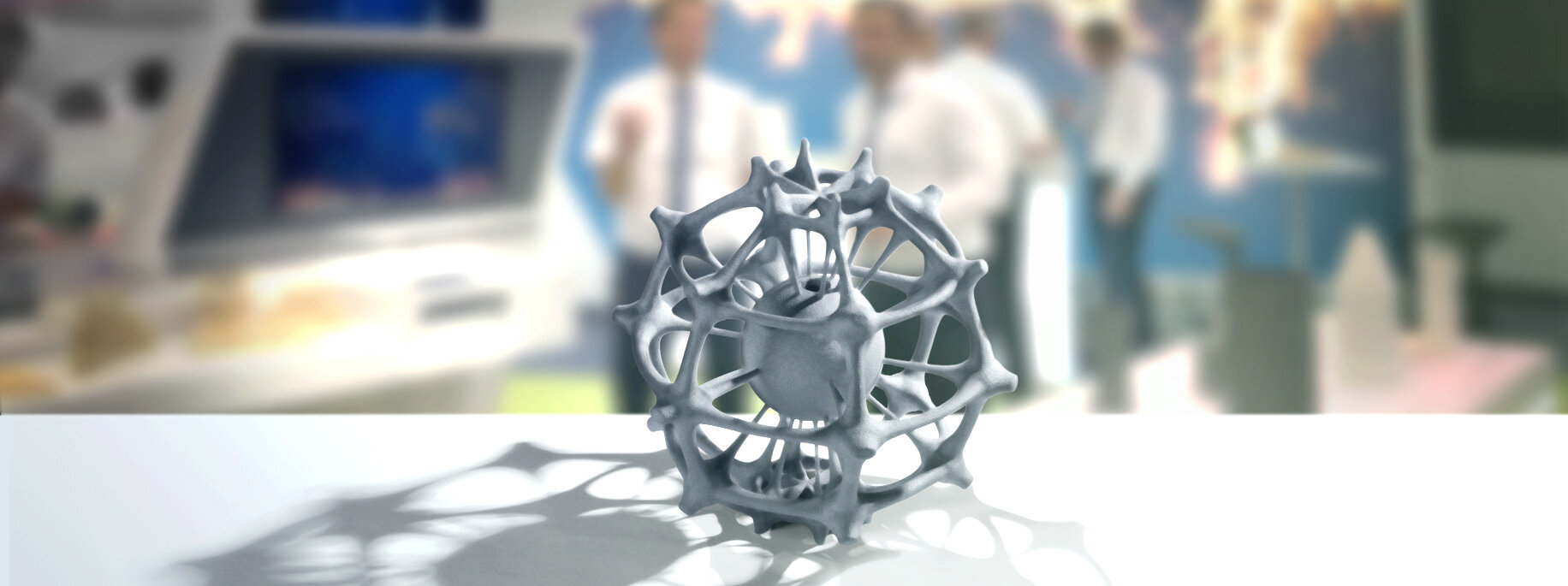
Schunk is elevating additive manufacturing to a whole new level. Because with IntrinSiC®, the 3D printing technique with silicon-carbide, components made of ceramic materials are now feasible in even more complex shapes, higher quantities, and in numerous sizes. Extremely temperature resistant, hard and shatterproof, RBSiC material stands out for its cost effectiveness and energy efficiency, and hence it facilitates the design of reliable production processes. Arising from the aspiration to meet the high demands of its customers, Schunk has succeeded in increasing the homogeneity of this extremely hard material, thus significantly improving the reliability and strength of the 3D printing parts produced with it.
In comparison with other methods, this technique permits the manufacture of considerably more complex and larger structures. It also eliminates the need for the time-consuming production of casting molds. Instead, geometries can be changed by a simple click of the mouse. In addition to its outstanding temperature resistance, RBSiC is also characterized by a high resilience to oxidation and corrosion, greater bending and creep strength as well as by its low density.
More safety through ceramic 3D printing
Since the global innovation IntrinSiC® was first presented in 2015, the further development of the material has opened up numerous new areas of application, for example protective ceramics. Inlets for protective helmets made from the advanced silicon carbide can even withstand hard-core bullets. Thanks to the innovative process and the extraordinary characteristics of the advanced ceramic, customized shapes are possible. The more homogeneous material and the associated increased strength ensure that the inserts can be optimally integrated into the head protection.
Ceramic 3D printing saves time and money
As a first mover in this sector, Schunk furthermore offers its expert knowledge as a service: the company supports its customers with the engineering design of components through the use of FEA (finite element analysis), in order to optimize reliability, weight savings and the properties of the mechanical structures.
Moreover, customers benefit from innovative IntrinSiC® technology thanks to higher degrees of process and design flexibility. Components can be immediately produced via CAD data, which permits short production-lead and delivery times possible. The surfaces of the diamond-hard material are immediately polishable.
Interested in more information?
→ Find all relevant brochures and documents on the topic here. Download now!