Market and innovation leader for ultrasonic metal welding
Minic-III Compacting
Compacting or final compaction of wires is an important step in the production of electrical connections, especially in control cabinet construction. Compacting increases conductivity and improves safety. But how can wire end compaction be carried out efficiently and reliably? The answer is: with Minic-III Compacting. The latest development in the field of wire end compaction offers numerous advantages over conventional methods. Minic-III Compacting is able to compact aluminum and copper cables with a cross-sectional area of up to 16 mm² and a compacting length of up to 20 mm. Ultrasonic welding technology is used to ensure the high quality and durability of the connections. The Minic-III Compacting is not only powerful, but also easy to operate. It requires no additional accessories. Many leading clamp manufacturers have already approved the Minic-III Compacting, confirming the positive trend towards ultrasonic welding technology. So if you are looking for an innovative and future-oriented solution for wire end compaction, then the Minic-III Compacting is just right for you. Contact us today to find out more about this unique product.
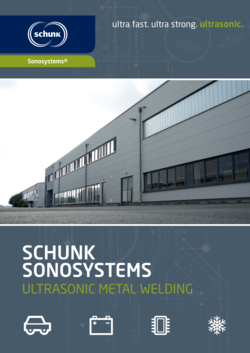
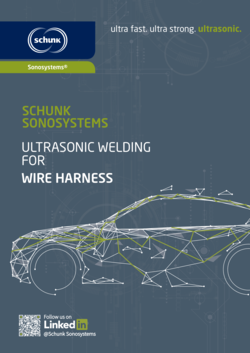
This brochure summarises all our wire harness machines.