Material Data Sheet for CarSIK-G
Silicon Carbide in Comparison
Silicon carbide is a chemical composite of silicon and carbon, which is one of the lightest and at the same time hardest ceramic materials. Silicon carbide ceramics differ depending on the manufacturing method, these include recrystallized (RSiC), sintered (SSiC), metal matrix bonded (e. g. SiSiC), metal reaction bonded (RBSiC), Si3N4 bonded (NSiC) and oxide bonded (e. g. mullitic bonded SiC). The ceramics have different porosities and densities. Schunk offers reaction bonded SiC (CarSIK-G, CarSIK-Z, IntrinSiC, CarSIK-GD, CarSIK-NT), nitride bonded SiC(CarSIK-NG) as well as mullite bonded SiC (CarSIK 70 ZA) and SSiC (CarSIK-SD).
Reaction-bonded Silicon Carbide
What distinguishes the reaction-bonded silicon carbide CarSIK-G, CarSIK-Z, CarSIK-GD and CarSIK-NT:
Compared to other SiSiC materials on the market, RBSiC from Schunk is characterized by a high secondary SiC content, which leads to significantly lower Si contents (<11 %) and thus higher bending strengths. The particularly resistant CarSIK-G, CarSIK-Z, CarSIK-GD and CarSIK-NT materials convince - in addition to the high bending strength compared to other RBSiC materials - with high temperature resistance, corrosion and wear resistance as well as low thermal expansion and high thermal conductivity.
Where are CarSIK-G, CarSIK-Z and CarSIK-NT used?
The very high thermal conductivity as well as temperature resistance in combination with a vanishingly low creep tendency make CarSIK-G a predestined material for burners and radiant tubes. Schunk's unique low silicon content of < 11 % in CarSIK-Z and CarSIK-G enables strength values that set it apart from the competition and allow the production of kiln furniture with the lowest thermal mass. Wherever energy is to be saved through reduced thermal mass and reliability is essential, CarSIK is the material of choice. Service lives of 10 years are not uncommon.
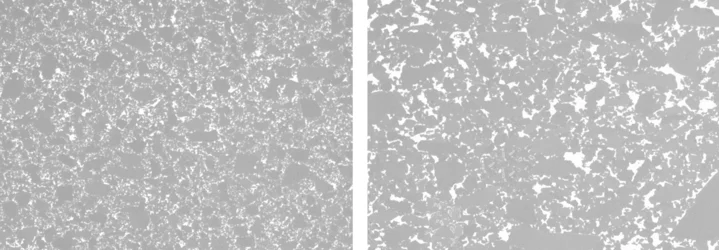
Special features
of CarSIK-G und CarSIK-Z
- Hardness: 25 GPa
- Density: 3,09 g/cm³
- Compressive strength: 1000 MPa
- Thermal conductivity-100°: 160 W/mK
- Flexural strength: 280 MPa
- Modulus of elasticity: 360 GPa
- Application temperature: 1380 °C
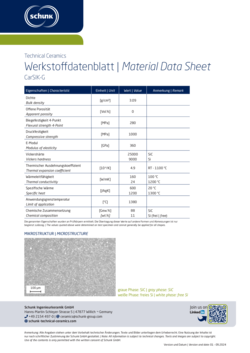
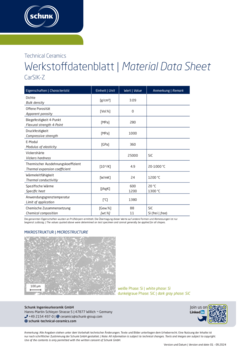
Material Data Sheet for CarSIK-Z
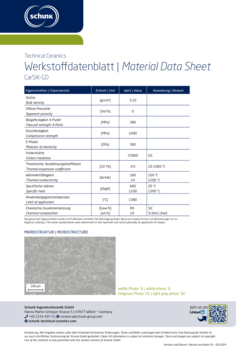
Material Data Sheet for CarSIK-GD
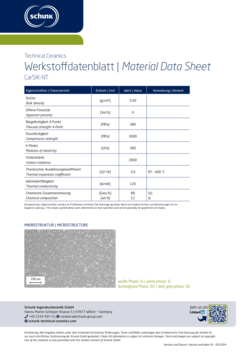
Material Data Sheet for CarSIK-NT
Downloads
Reaction-bonded Silicon Carbide IntrinSiC® from the 3D printer
Reaction-bonded silicon carbide IntrinSiC® (3D-printed):
With IntrinSiC®, we are redefining the dimensions in 3D printing: For the first time, ceramic components made of nearly diamond-hard silicon carbide (RBSiC) are possible via 3D printing, which were previously not feasible due to their size, complexity and quality requirements.
What makes IntrinSiC® stand out?
All the very good properties you are used to from Schunk's RBSiC are transferred to the new dimension of 3D printing by IntrinSiC. IntrinSiC® is characterized by enormous stiffness and strength, low thermal expansion, high Weibull values and temperature resistance, low thermal mass and high hardness.
Where is IntrinSiC® used?
IntrinSiC® is used wherever complexity and size are relevant: Machine frames, diffusion furnaces, complex high-performance burners, body protection panels, aviation protection panels as well as helicopter seats. Thanks to the freedoms of 3D printing, previously unfeasible geometries and undercuts are possible. Weight-optimized components can be produced in sizes up to 1.8 m x 1.0 m x 0.7 m as a monolithic component. The combination of low thermal expansion with high thermal conductivity, very high stiffness and high Weibull modulus also make IntrinSiC® the perfect solution for space applications and measuring machine components where the highest precision is required.
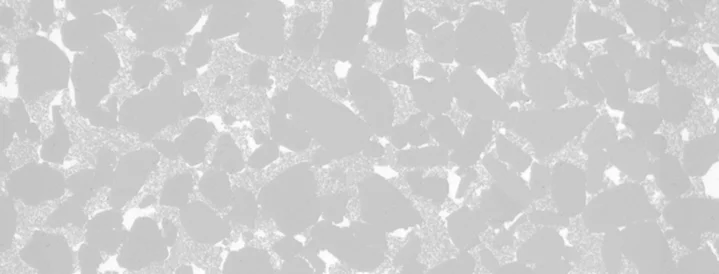
Special features
of IntrinSiC®
- Density: 3.05 g/cm³
- Weibullmodul: 14
- Coefficient of thermal expansion [10^-6/K] 3.9
- Thermal conductivity(room temp.): 200W/mK
- Flexural strength: 210 MPa
- Modulus of elasticity: 380 GPa
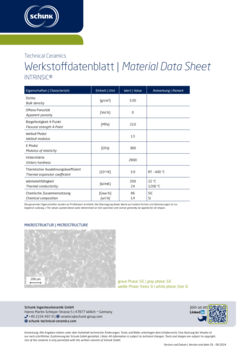
Material Data Sheet for IntrinSIC
Downloads
Nitride-bonded Silicon Carbide
Nitrite-bonded silicon carbide (CarSIK-NG):
NSiC belongs to the porous silicon carbide ceramics with 10 - 15% porosity (< 1% open porosity), which give the material good thermal shock resistance. The silicon nitride matrix additionally protects the material from oxidation and allows it to be used even in air up to 1470 °C. Schunks NSiC is marketed under the brand name CarSIK-NG.
What distinguishes CarSIK-NG?
Compared with RSiC, CarSIK-NG is characterized by a smaller pore size, which means significantly higher flexural strength as well as surface resistance without deformation - even over a longer period of use. The material has thus proven itself as a highly resilient and durable kiln furniture up to 1,470 °C. Coupled with Schunk's unique manufacturing expertise, the production of plates up to 1 m x 0.8 m is possible. Thanks to the silicon nitride matrix, products made of CarSIK-NG are poorly wettable by non-ferrous metal melts. This enables use in direct contact with zinc, but also aluminum and tw. copper melts.
Where is CarSIK-NG used?
Due to its high temperature resistance, thermal shock resistance and low density (2.85 g/cm³), CarSIK-NG is predestined for use as a kiln furniture in the oxidative range for firing ceramic products. Especially in sanitary ceramics, but also in technical ceramics, CarSIK-NG is the material of choice for lightweight, long-lasting kiln furniture plates. Its low wettability to metallic melts also allows it to be used as an immersion tube for heating melts by means of gas burners. Due to its low thermal expansion and good strength, CarSIK-NG is also suitable for use in measurement technology, e.g. as a quill.
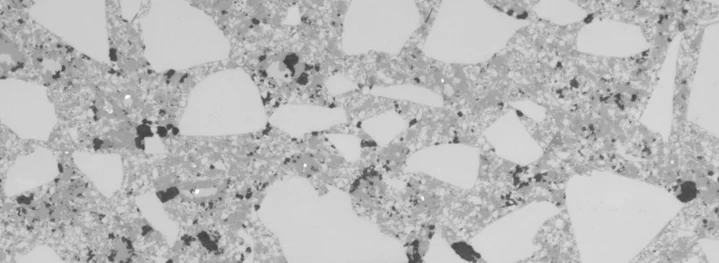
Special features
of CarSIK-NG
- Density: 2.85 g/cm³
- Thermal conductivity: 12 W/mK
- Flexural strength: 200 MPa
- Modulus of elasticity: 220 GPa
- Application temperature: 1470 °C
- Coefficient of thermal expansion: 4.6 x 10^-6
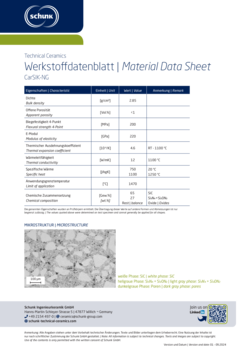
Material Data Sheet for CarSIK-NG
Downloads
Mullite-bonded Silicon Carbide
Mullite-bonded silicon carbide (CarSIK 70 ZA):
Mullite-bonded SiC is characterized by good electrical insulation, thermal and chemical resistance, comparatively low thermal expansion, and high thermal shock and corrosion resistance.
What distinguishes CarSIK 70 ZA?
CarSIK 70 ZA impresses with its high thermal and chemical resistance, mechanically robust structure and high thermal shock resistance, and also has a good price-performance ratio.
Where is CarSIK 70 ZA used?
In aluminum die casting plants, tubes made of CarSIK 70 ZA (available in a wide range of extruded diameters, open or closed) effectively protect the heating elements against contamination and splashes of molten aluminum. Mechanical-corrosive damage is thus prevented.
Special properties of CarSIK 70 ZA:
- Open porosity: 25
- Density: 2,1 g/cm³
- Application limit: 1400 °C
- Coefficient of thermal expansion: 5 [10-6 K-1].
- Thermal conductivity: 7 W/mK
- Flexural strength: 30 MP
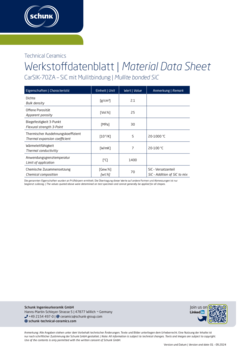
Material data sheet for CarSIK-70ZA
Downloads
Silicon Carbide from Chemical Vapor Deposition
Silicon carbide from chemical vapor deposition (CVD-SiC):
The unique CVD SiC technology, which Schunk markets under the name P 60, is used to produce components that are characterized by high corrosion, oxidation and heat resistance as well as wear resistance. By combining CVD-SiC coating with IntrinSiC, they have the capabilities to create almost any geometry and finish it by P 60.
What distinguishes P 60 CVD-SIC coatings?
The high purity, low thermal expansion and good mechanical properties open up new possibilities in the semiconductor industry. The contamination of wafers by any impurities from the substrate or its surface is thus avoided, for example.
Where is the P 60 CVD-SIC coating used?
For satellite technology, lithography and diffusion furnaces, Schunk's CVD-SiC manufacturing technology with an exceptional purity of 99.9995 % is indispensable today. Schunk Ceramics also offers CVD-SIC coating for particularly large components.
Special properties of CVD-SiC:
- Density: 3.18 g/cm³
- Porosity: 0 %
- Electrical resistivity: 1500 μΩm
- Degree of oxidation: 4 x 10-6 mg/mm2 x h
Sintered Silicon Carbide
Sintered silicon carbide (SSiC):
Pressureless sintered silicon carbide (SSiC) is a particularly light and at the same time hard high-performance ceramic. SSiC is characterized by high strength, which remains almost constant even at extreme temperatures. Schunk offers SSiC under the names CarSIK-SD.
What distinguishes CarSIK-SD?
Schunk's CarSIK-SD has a very high resistance to chemical corrosion. Exceptionally high hardness combined with low density is optimal for lightweight solutions.
Where is CarSIK-SD used?
Thanks to its excellent properties, our SSiC ceramic is used in sliding and sealing rings. In personal protection and for the armoring lining of land and air vehicles, CarSIK-SD is also suitable.
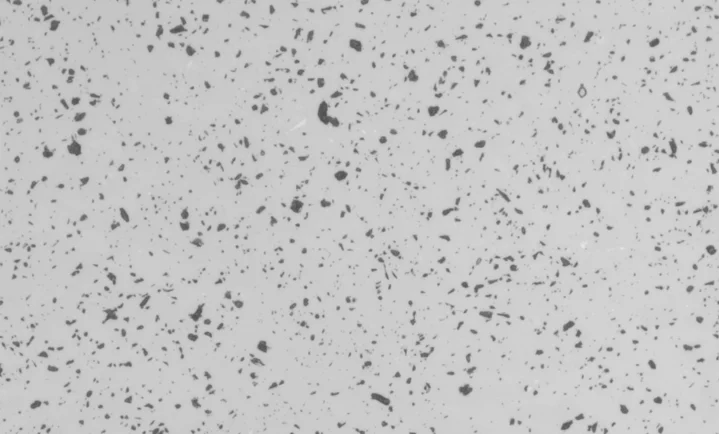
Special properties
of CarSIK-SD (SSiC)
- Hardness: 28 GPa
- Density: 3,1 g/cm³
- Compressive strength: 3800 MPa
- Thermal conductivity: 110 W/mK
- Flexural strength: 390 MPa
- Modulus of elasticity: 400 GPa
- High corrosion and wear resistance